Porosity in Welding: Identifying Common Issues and Implementing Finest Practices for Prevention
Porosity in welding is a pervasive issue that frequently goes unnoticed till it triggers significant problems with the honesty of welds. This typical problem can compromise the toughness and longevity of bonded structures, posturing safety and security dangers and leading to pricey rework. By comprehending the root creates of porosity and carrying out effective prevention methods, welders can substantially improve the quality and integrity of their welds. In this discussion, we will explore the crucial aspects contributing to porosity development, examine its destructive impacts on weld efficiency, and talk about the very best practices that can be taken on to minimize porosity event in welding processes.
Common Sources Of Porosity
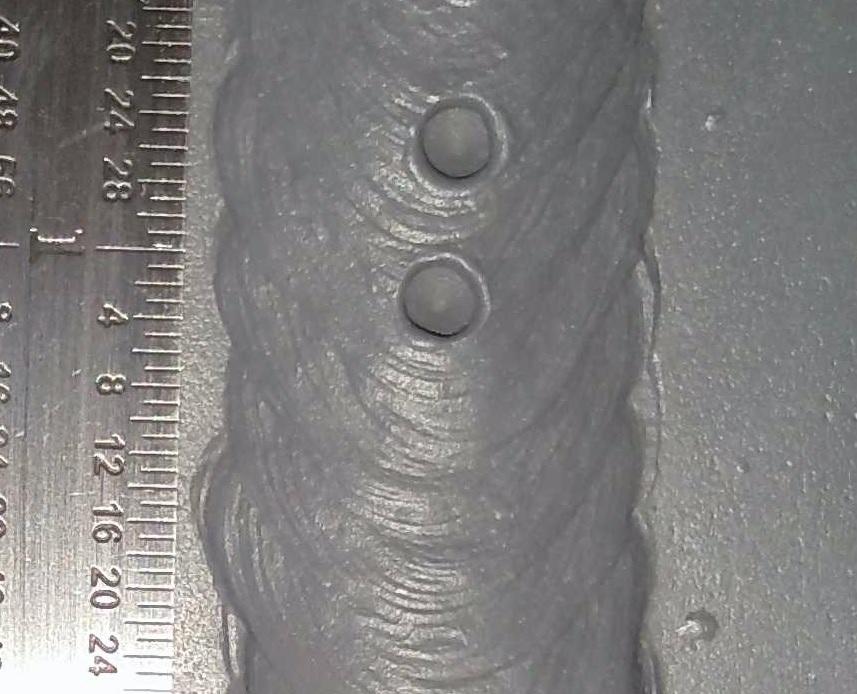
Another frequent wrongdoer behind porosity is the visibility of impurities externally of the base metal, such as oil, grease, or rust. When these pollutants are not successfully eliminated before welding, they can evaporate and end up being entraped in the weld, triggering flaws. Using dirty or damp filler products can introduce impurities right into the weld, adding to porosity problems. To reduce these common root causes of porosity, detailed cleansing of base metals, proper securing gas choice, and adherence to ideal welding parameters are important methods in accomplishing high-quality, porosity-free welds.
Impact of Porosity on Weld Top Quality

The visibility of porosity in welding can dramatically compromise the architectural honesty and mechanical buildings of bonded joints. Porosity produces gaps within the weld steel, weakening its total stamina and load-bearing capability. These spaces act as stress focus factors, making the weld much more vulnerable to fracturing and failing under applied tons. In addition, porosity can reduce the weld's resistance to rust and various other ecological aspects, better decreasing its durability and efficiency.
Among the More Help key consequences of porosity is a decrease in the weld's ductility and strength. Welds with high porosity degrees often tend to show reduced influence stamina and decreased ability to deform plastically before fracturing. This can be especially concerning in applications where the welded elements go through dynamic or cyclic loading conditions. Moreover, porosity can restrain the weld's ability to properly send pressures, bring about premature weld failing and prospective security dangers in important frameworks.
Best Practices for Porosity Avoidance
To enhance the structural stability and high quality check this of bonded joints, what specific steps can be carried out to decrease the event of porosity throughout the welding process? Making use of the correct welding strategy for the specific material being welded, such as adjusting the welding angle and gun setting, can additionally stop porosity. Normal examination of welds and prompt removal of any type of concerns identified during the welding process are vital methods to stop porosity and additional resources create top notch welds.
Relevance of Correct Welding Methods
Carrying out appropriate welding methods is extremely important in guaranteeing the structural honesty and quality of bonded joints, constructing upon the structure of efficient porosity prevention steps. Welding techniques straight influence the general stamina and durability of the welded structure. One key aspect of correct welding strategies is preserving the correct warmth input. Excessive warmth can cause enhanced porosity due to the entrapment of gases in the weld swimming pool. Conversely, not enough warm may cause incomplete blend, producing potential weak factors in the joint. Furthermore, using the appropriate welding specifications, such as voltage, current, and take a trip speed, is essential for attaining sound welds with marginal porosity.
Additionally, the choice of welding process, whether it be MIG, TIG, or stick welding, must align with the particular requirements of the job to make certain optimum results. Proper cleaning and preparation of the base steel, in addition to choosing the appropriate filler material, are likewise crucial components of efficient welding techniques. By sticking to these ideal practices, welders can minimize the risk of porosity formation and generate top notch, structurally sound welds.
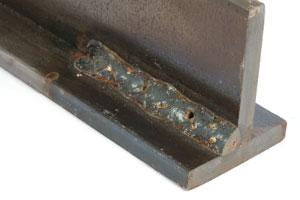
Examining and Quality Assurance Actions
Quality control steps play a critical duty in verifying the integrity and reliability of welded joints. Evaluating procedures are essential to identify and prevent porosity in welding, guaranteeing the stamina and toughness of the last item. Non-destructive screening methods such as ultrasonic screening, radiographic testing, and aesthetic assessment are frequently utilized to determine prospective problems like porosity. These strategies permit the analysis of weld top quality without compromising the stability of the joint. What is Porosity.
Post-weld examinations, on the other hand, evaluate the last weld for any problems, consisting of porosity, and validate that it fulfills defined requirements. Executing a comprehensive top quality control strategy that includes thorough screening procedures and inspections is extremely important to reducing porosity problems and making sure the total top quality of welded joints.
Verdict
To conclude, porosity in welding can be a typical issue that influences the high quality of welds. By recognizing the usual sources of porosity and applying ideal techniques for prevention, such as correct welding techniques and screening procedures, welders can make certain top quality and trusted welds. It is vital to prioritize prevention approaches to reduce the occurrence of porosity and maintain the integrity of welded structures.